Progress
In week 12, I had progress in integrating all the electrical stuff by capturing and soldering all components to a PCB board. In addition, I worked with Max in mechanical integration.
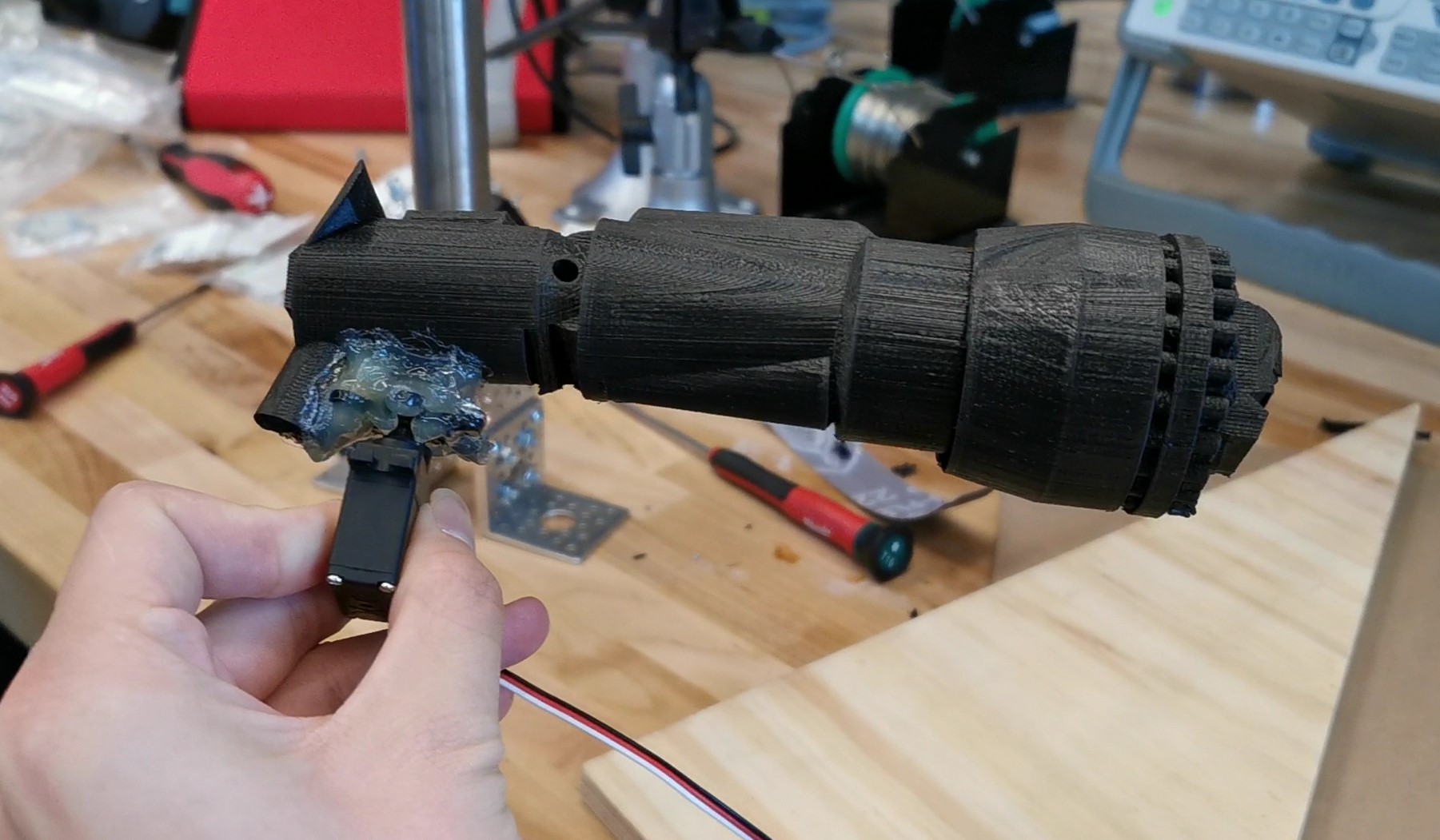
3D Printed IR Man Arm Driven by Servo
The IR Man Arm was printed in PLA. And I have concept proven with driving the motion of the 3D printed Arm with a servo (in terms of torque, speed, and precision). It worked really well and we are going to proceed to print the rest of the IR Man body in this following week.
On the other hand, all the electrical components have been captured and soldered onto a PCB, marking the end of the breadboarding stage. Completed unit testing the newly soldered PCB boards and all functionalities works as expected. In this layout design, I inserted a breakout socket that allows up to 6 IR diodes to be connected in parallel. The electrical integration added more protection to the RPi and the fragile GPIOs, and also added mobility to the platform.
Schedule
This week’s development is on schedule. Now shifting more focus to mechanical design and integration. Also, need to work on motor control for different scenarios and device location function on the client code.
Deliverables Next Week
- CV Image Post-processing
- Client Code Modification -> Device Location Func
- Motor and Servo Motion Development
- Scenarios Modes and Programming
- More Mechanical Parts Assembly
- Mechanical Design: Integration and 3D printing IR Man Body
- Figure out how to mount RPi and IR Man onto rotating base
- Mounting all the wires, IR circuits, Cameras onto IR Man Body
- Paint IR Man with color
- Benchmark Testing and Metrics Reports for each MVP
0 Comments