During class this week, I watched other groups’ project proposals and found them to be really interesting. I spent some time on Sunday to help finish up our presentation with the group.
One point that was brought up during the discussion after our presentation was why we were using a claw as our end effector rather than a vacuum gripper. I had previously given the vacuum-powered gripper some consideration but wanted to re-evaluate that choice just in case. In my research, I found that the most reasonable methods to do this given our use case was either using a squishy universal gripper or a suction gripper. However, the squishy universal gripper is better suited when pressing against a smaller object, which does not match our use case. The universal gripper typically molds around the object and holds the mold by vacuuming out the remaining air. The objects we are picking up will not have much normal force opposing the force we apply (since they are freestanding in a shelf) and will not be small, so the universal gripper will not work. The suction gripper will also require a very strong and expensive vacuum pump that is not practical for us to purchase. Typical off-the-shelf vacuum systems seem to only be able to carry 0.22 lbs, so it will not perform well enough.
After the above research, I decided to proceed with the servo-powered claw end effector idea. I have yet to solidify the linear actuation method but believe I will likely be using a DC motor-powered linear slide system. With this in mind, I wanted to sketch out the electronics required for my end effector and linear actuation systems. I chose a standard PWM servo and I2C servo driver (specifically PCA9685 in the diagram) for the claw. I chose a H Bridge motor driver and DC motor for the linear actuation system. Both of these choices were inspired by many other Jetson Nano projects I saw using a servo or DC motor, and I wanted to focus on feasibility before refining my choice of hardware.
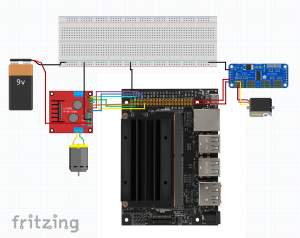
However, I realized that the battery needs significantly more consideration than I had previously considered. This is because there are many ways to power the Jetson Nano which requires 5V/2A (10W) while the DC motors will require 12V and the servos require 5V (share the same power source as the Jetson Nano). We can either have different power sources for the motors and Jetson Nano or use a buck converter. I have been heavily evaluating the tradeoffs as the Jetson Nano seems to be sensitive about battery sources (i.e. read a lot of articles indicating that the USB power bank source should be avoided). For now, I left the power source for the Jetson Nano out of the diagram but have been focusing a lot of research in this area.
I believe I am currently on track with researching design considerations. After finishing up my research on electronic components, I will move onto CADing the mechanical components.