Skip to content
- Week recap
- CAD models for the lift system
- 3D print gears to get our desired torque output from the steppers (each stepper needs to lift 5lbs)
- Initial version of complete, and will be submitted for fabrication on Monday (see image below)
- Plan is to mount these between 1/4″ plywood panels that will make up the arms of our lift system
- Decided on using cams fixed to large gear to lift bins for easy positioning
- Roomba driving
- Was having trouble getting it to enter serial communication mode
- Potential default baud rate issue (115200 stated in documentation)
- Using special boot procedure for reliable 19200 baud comms
- Tethered driving with computer: Drive Code v0
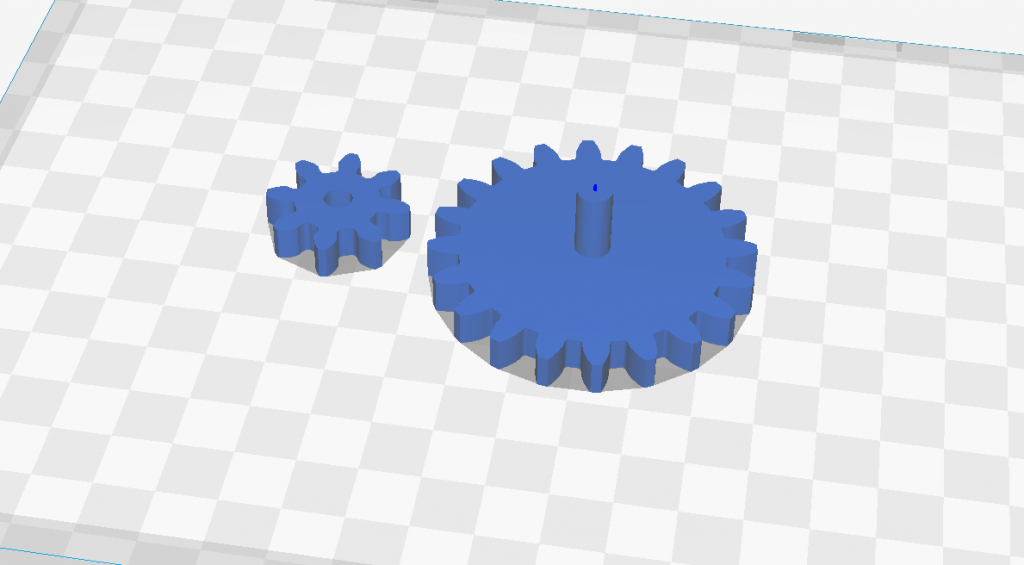
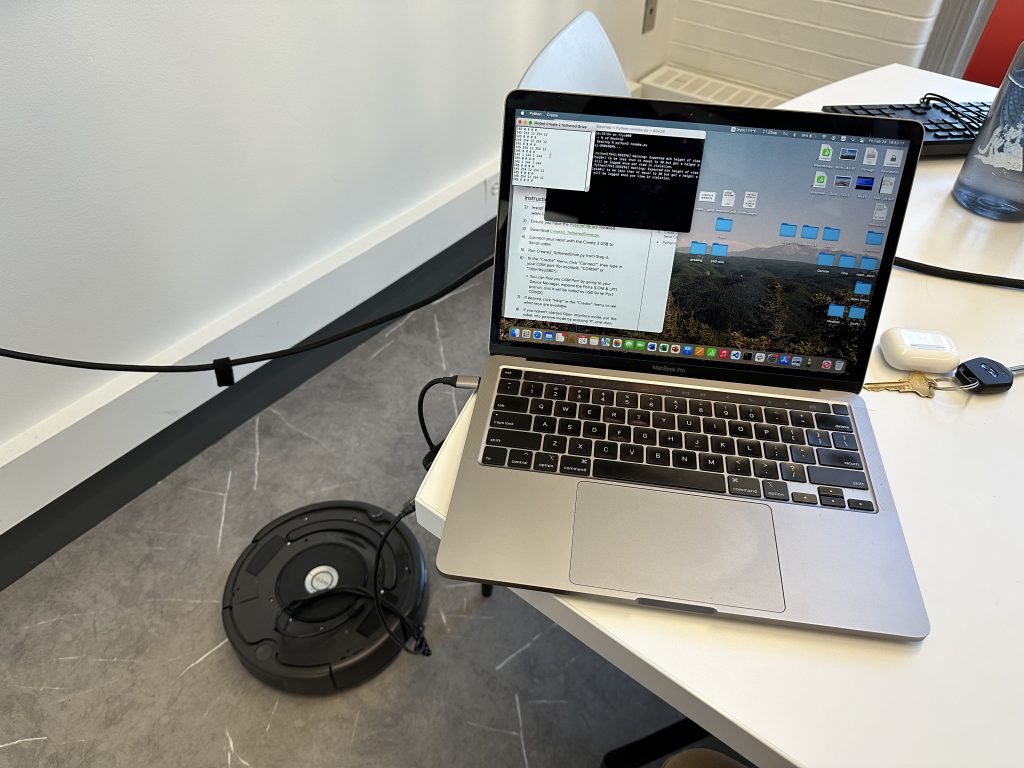
- Schedule
- Slightly behind on CAD for docking system
- Good trajectory this past week, which will be carried forward
- Validate prototype gears and move to full version with cams (rapid progress here)
- Getting more used to Solidworks again
- George assisting with stepper motor control
- Any redesign work can happen over spring break and use slack time for further testing
- Deliverables next week
- Working prototype of the pickup arms, with mount points for gears
- Gear system validation
- If gear testing is successful, make/print the next iteration with cams, otherwise make gearing changes to reach target lift capacity
- May write code with a simpler interface for roomba driving, with more customization on motor speeds (dependent on other group member needs)