Tests
Response Time:
We found that we had a response time of 50ms. This estimate is what we found to be a ceiling estimate of the longest response from the carrier to track. Based on the results we believe that we should be able to position the stops between the carrier and coil to be able to account for the delay and properly propel the coil in a sightly manner. We anticipate that the Arduino response time will be somewhat variable and should be fast enough for our needs despite the added delay that comes from the serial Bluetooth communication. No design changes are needed based on the results of this test.
Risks
Speed-Up Coil:
When it comes to the coils, it seems like the height of the coil is to big for the carrier to pass over, which was not anticipated until recently as previous tests showed that just the carrier itself could go over the coil, but now with the circuitry added and weight being an issue now, this is a risk since if the coil isn’t short enough, then we run into the issue where the carrier would just stop at the speed-up coil, and not be accelerated by the coil, which are detrimental to the project. The point of the coil is to allow the carrier to be propelled across the track and if the height is an issue such as now, then we can not propel the carrier across the track. With this being an issue, we arrear now looking into altering the design of the spool for the coil as well as considering other changes like reducing components on the carrier as well as removing the battery form the carrier in order to reduce the weight of the carrier which would then increase the levitation from the track for the carrier, which would then allow the carrier to pass over the coil easily.
Design Changes
Decided to go with a smaller height for the speed-up coil spool in order to allow the carrier to pass over the coil when traveling on the track, since weight is now a huge factor to this project.
Schedule
No change in our schedule.
Test
Response Time:
We found that we had a response time of 50ms. This estimate is what we found to be a ceiling estimate of the longest response from the carrier to track. Based on the results we believe that we should be able to position the stops between the carrier and coil to be able to account for the delay and properly propel the coil in a sightly manner. We anticipate that the Arduino response time will be somewhat variable and should be fast enough for our needs despite the added delay that comes from the serial Bluetooth communication. No design changes are needed based on the results of this test.
Speed Up Coils
When it comes to testing the speed-up coil, we tested which coil produces the most magnetic field based on the radius, the type of AWG Copper Wire, the amount of current going through the coil, turns, etc.
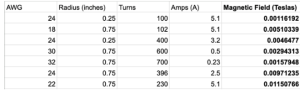
With these results, we can easily tell that the coil with 22 AWG with a radius of 0.75 inches, 230 turns and 5.1 Amps which produces .012 Tesla, that this coil is the one that produces the most magnetic field. When it comes to the final product, we know that this coil produces a powerful magnetic field, but we need to consider the smoothness of the carrier when it passes over the coil. With that being said, we tested where on the coil the back end of the carrier should be positioned to maximize smoothness and distance traveled from the propulsion. We marked the spool with a sharpie and confirmed visually that the carrier can smoothly travel about one section of the track in length without nose diving and maintaining stability.
Levitation and Stability
The remainder of our test was completed through visual inspection. We looked at how well our carrier levitated and propelled on the track to determine whether they meet our standards. For levitation, we wanted our carrier to continuously levitate regardless of its location on the track. With our final design—2cm magnets with no spacing for the carrier and 2.5 cm rectangle magnets no spacing for the track—we were able to achieve this. For stability, we wanted our carrier to continuously and evenly propel, regardless of location on the track. This was also achieved with this current prototype. Past prototypes magnet shapes caused parts of the track to be attracted to edges of the magnets, causing irregular propulsion. The new design has eliminated this issue.