In the near future, we envision the electromagnet not initially working and the camera lens being distorted at the edges being our most significant risks. We are planning on mitigating these risks by spending more time debugging the firmware and hardware on the MCU, the robot PCB, and the electromagnet and trying to understand why our electromagnet could not attract a paperclip. We found resources from manufacturers, namely Seeed and Keyestudio, about how to use their products with an Arduino, so we are confident that it should work soon. For the camera, we are going to have to calibrate the camera by moving a robot (with lit neopixel LEDs) in relation to a fixed camera and determining how the lengths between the centers of the LEDs change based on where the robot is. From there, we will have an idea of how the camera lens is curved at the edges compared to the center of view.
We are moving the robot field construction to the coming week, but everything else on the schedule should stay the same. As of now, we do not have any changes to the design or requirements, but we are reviewing and discussing the feedback that we got from the proposal presentation.
We got PCBs back this week and did an initial fit test: 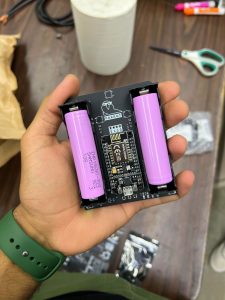
Then, we reflowed and assembled three robots:
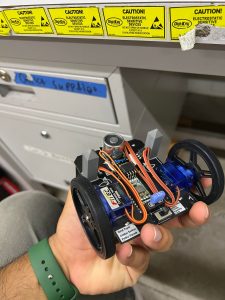
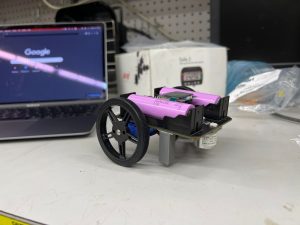
We also got the screen working:
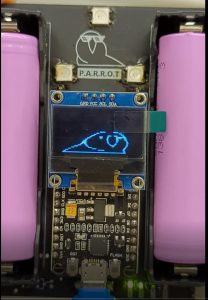