This Week:
This week I put the finishing touches on the gantry. This mainly included laser cutting wood and attaching it to the frame. While this sounds trivial at worst, it unfortunately wasn’t.
First, we didn’t buy enough wood. The 4x4ft sheet was a hair too short to get a third cut: 4ft ~ 122cm and our longest dim for the footprint is 69cm, so we were just 16cm short. As such, I needed to go and find where I could buy such an awkward size of wood. Techspark only sells 1x2ft increments, which are far too small, and going through home depot again would have been a headache between picking up, and cutting down a 4x4ft sheet again so it could fit in the laser cutter. Further, this would eat into the last remaining pennies of our budget and be super inefficient (54*69 / 122^2) = 25% used of the whole sheet. Thankfully, after bothering Ed (Techspark guy) enough, I was able to scavenge a 2x3ft sheet of a very similar wood to what we already bought.
Second, laser cutting / engraving large patterns takes forever. The top panel with only the small logo in the corner took 10 minutes, and the base with a lower resolution etch took 30 minutes. The whole time I had to stand watching the laser cutter, so couldn’t do anything else.
Third, because we are attaching this wood to the frame, I need inserts. However, the inserts I printed are out of the rails, and the only way to get them into the rails is to disassemble a large amount of the frame, as well as reseating the belt. And to make things worse, I had to stop working and come back to do the baseplate after the top, so I had to do the whole disassembly twice ;-;. Thankfully, nothing broke, but it took several hours to get that done.
Lastly, there were no screws long enough to properly raise the top plate off the stage. After much scavenging through techspark, I found a bunch of 8cm long imperial bolts. However, there were two problems with them. First, they were too wide, so I needed to widen several dozen holes through various parts to get the new bolts to fit. Second, they were shanked bolts (there’s a smooth section between the head and the start of the threads). In this case, it was about half shank (4cm shank, 4cm threads). So my original plan to just use a nut to hold the top wood up wouldn’t work. After much testing, I found that using hotglue to gum up the holes in the wood and then shoving the bolt in while the glue was still warm caused enough friction to hold the bolts in place. At least, well enough. So after 30+ minutes of just hot glueing and bolting holes, I had the top board done.
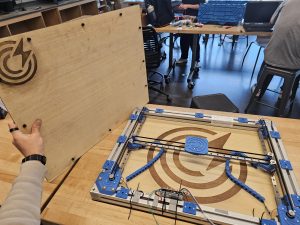
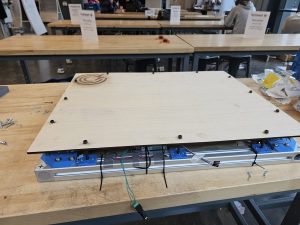
Schedule Changes:
Not enough time left in the semester to really have a schedule. As of right now, I’m basically done with everything I needed to do. I’m just waiting on Cal and Anirud to finish the sensor array, at which point I will assist with final assembly.
Next Week:
I’ll assist with final assembly once the sensor matrix work.