I assembled the entire jacket, with waterproofing, cable management, and fully soldering all components. We tested the jacket, and all functionality seems good. The only part we’d add to the jacket is perhaps a case for the battery and board circuit.
Images below from top to bottom: the jacket board, debugging the circuit, heatshrinking for cable management and waterproofing.
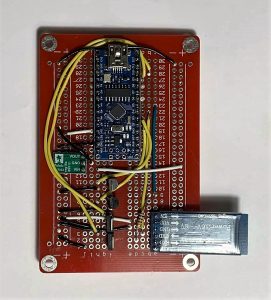
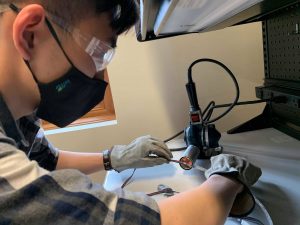
I have been working on the rest of the Solidworks models. There are a lot of components, but so far it seems like they are fitting together nicely. We decided to have 3 main boxes on the bike. The main challenge with the models is that we have precise angles for the sensors, which takes more precise modeling. Fortunately, Solidworks provides the tools to fully define everything to precision. Below is a view of the back box of the bike.
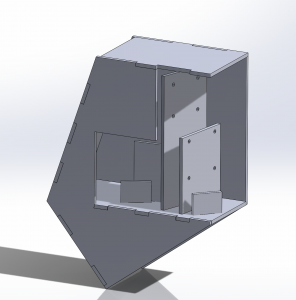
I have only fully finished the back, but the front box should have similar components to the back box, so that should be easier to do. The 3rd box contains the battery, which is just a simple box with USB cable cutouts.
I will laser cut all the components this week and assemble everything. Then, I will mount the boxes onto the bike, which should complete the construction phase of the project, leaving us a couple weeks to do testing.