What did you personally accomplish this week on the project?
This week I met up with Alycia to get feedback on the design direction we should be going in for the Braille embosser. I asked her about how she can distinguish between different sides on a box, because we will need to be able to load paper in a specific direction on the printer. She mentioned different way of adding tactile information like adding an arrow to where the embosser needs paper inserted.
She also gave us the opportunity to use her different accessibility tools on her iPhone, and I have to say I’m pretty impressed with how easy it is for her to navigate around on her iPhone with her braille input device. She was able to navigate around Wikipedia and search up information about Beyonce no problem. She also showed how certain menu displays are not accessible to her, and aired some grievances about the Dunkin Donuts app and their inaccessible app.
I learned so much from Alycia this week, and I think her involvement in the project will steer us towards making a project that is actually useful to blind users. She took the time to show us the different tools she uses in her day-to-day life and that gave us some ideas on things we can integrate into the software side of the project. Specifically, she showed us these glasses she uses to read text, and detect scenes, which integrate already into her phone and could be a cool tool to integrate into our project because she could take a box with instructions, look at it with her glasses, and then take the text output from the glasses, and convert it into braille. Here’s a pic of me trying these glasses on at Panera Bread this week.
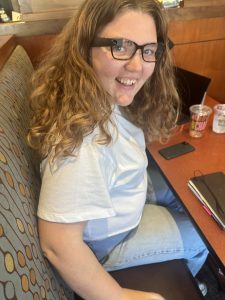
I started exploring how the gantry system was actually going to get constructed, and realized very quickly that designing our own system from scratch would be really expensive in terms of time, effort, and money to create, and that it would be a better use of time to buy a x/y system that was already built. I ended up finding a 3D printer for 135$ on Amazon that would have all of the mechanical parts we would need to print braille, and most of the electronics already included. When I looked into 2D plotters they were more expensive, and also may not be the best choice because we want to be able to control the amount of tension we have between the paper and the embosser.
I think using the 3D printer kit would come with many advantages including:
- X/Y mechanical movement already figured out (saves time & $$$ on prototyping)
- Electronics have JST connectors we can plug into our control board for easy wiring
- We can control the Z-height of the embosser, which will be good for finding optimal tension between the paper and the embosser. It also gives us a lot of flexibility when designing the embosser
- Parts already integrate into the RAMPS based control system we plan on using.
Like any other decision, using this kit will have its’ drawbacks.
- The z-height is much taller than we need it to be. We can cut this piece, but that will require us to disassemble and reassemble the x/z gantry
- We will need to figure out a way to make it easy to register the paper (consistently place the paper in the exact same location) in a way that is accessible to our user. I think we can accomplish this by creating a easy to use slot based system.
- We will need to modify the slot where the extruder goes to fit the solenoid.
If we were to source our own parts, it would be so much more expensive to build, to the point where it wasn’t worth finishing the spreadsheet.
DIY assembly |
Cost |
Quan |
Total |
Link |
Nema 17 motors |
8.99 |
3 |
26.97 |
|
Linear slide + mount |
37.99 |
3 |
113.97 |
|
limit switches |
|
|
|
|
tensioner |
|
|
|
|
t slot |
|
|
|
|
Nuts & screws |
|
|
|
|
T-Slot Brackets |
|
|
|
|
ETC |
|
|
|
|
|
|
|
|
|
|
|
ALT TOTAL |
140.94 |
|
Using the 3D printer kit will take some work to modify. We will need to do the following to create a system that meets our requirements:
- Creating a mount for the embossing solenoid to go on the X/Z gantry
- Making an accessible registration system
- Creating an enclosure for the 3D printer so it is safer to use
- Integrate the electronics to the ramps board
- Figure out how to control the solenoids on the ramps board
- Figure out how to communicate with the software portion of the project
I started exploring how we will control the system as a whole, and there is a way to control the 3D printer using G-Code on the RAMPS board. We will be able to modify the firmware to meet our hardware needs, as they have a way to add solenoids. I think we will be able to also add a setting to keep the embosser head at a specific height, depending on the tension that works best for printing.
I also started exploring how to communicate with the RAMPS board over Wi-Fi, and there is this software called Octo-Print that runs on a raspberry pi can control a 3D printer. I will need to do more research to see how we can integrate it into our software system, but it is a good sign that this exists.
Is your progress on schedule or behind?
I feel like I’m making good progress on the project, and I think this week we can actually make some tangible progress if we can get the 3D printer ordered this week.
What deliverables do you hope to complete in the next week?
- Order the 3D printer kit, and RAMPS Controller
- Put in a request for a raspberry pi
- Come up with a specific plan to communicate with the 3D printer over wifi
- Design PCB’s that make connecting the limit switches, solenoids, and any other auxiliary hardware easy to plug into the ramps board.