This week, we all worked on full scale integration with the hardware and the Raspberry Pi. This involved making sure the board could detect every single piece and could accurately determine the legality of a move and when a game should end. We initially had success, but later had some issues with the ADC on Wednesday. On Saturday, I was able to solve the problem by changing the way the “chip select” line was toggled in our setup. At this point, the process of piece detection, move detection, and legality checking works to our expectations.
In terms of the board mechanical aspects, our remaining magnets arrived this week, so we were able to finish assembly on the last pieces and test the board with every single piece on the board. I was also able to set up the Pi to have the whole system powered off of the board’s battery pack instead of needing an outlet for the Pi.
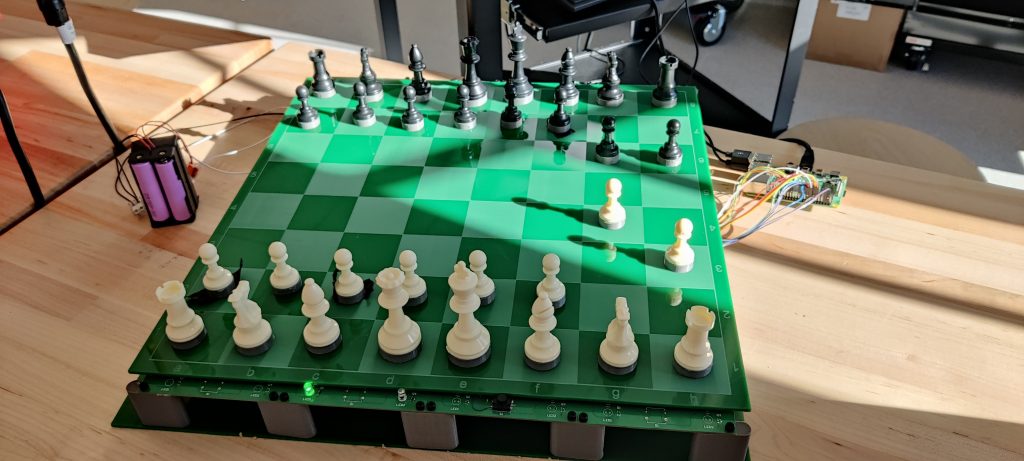
Given all of this progress, we were able to test both accuracy and power consumption with the expected load. The board was able to detect all moves accurately, and the power consumption is in line with what I predicted based on the Pi’s theoretical power use.
With this progress, we used some of the slack time, but have largely finished the final integration portion of the project. Any remaining small details will be ironed out next week before the demo.
In the next week, I will re-glue some of the pieces to make them more secure. I will also add some tape or latex to the bottom of each piece to increase the friction between the pieces and the board. This will prevent any pieces from interacting due to magnetic forces between themselves.
Recent Comments