Lots and lots of CADs and laser cutting.
All the small misalignments between parts have been fixed using wooden pieces joined together with joints and hot glue. For example, initially, we decided to stick all parts onto the machine permanently, but we discovered that it would be better to have them be detachable. So, I made a detachable wooden case for each of them to hold them in place. There are more of these very small changes that were mostly done using laser-cut wooden parts.
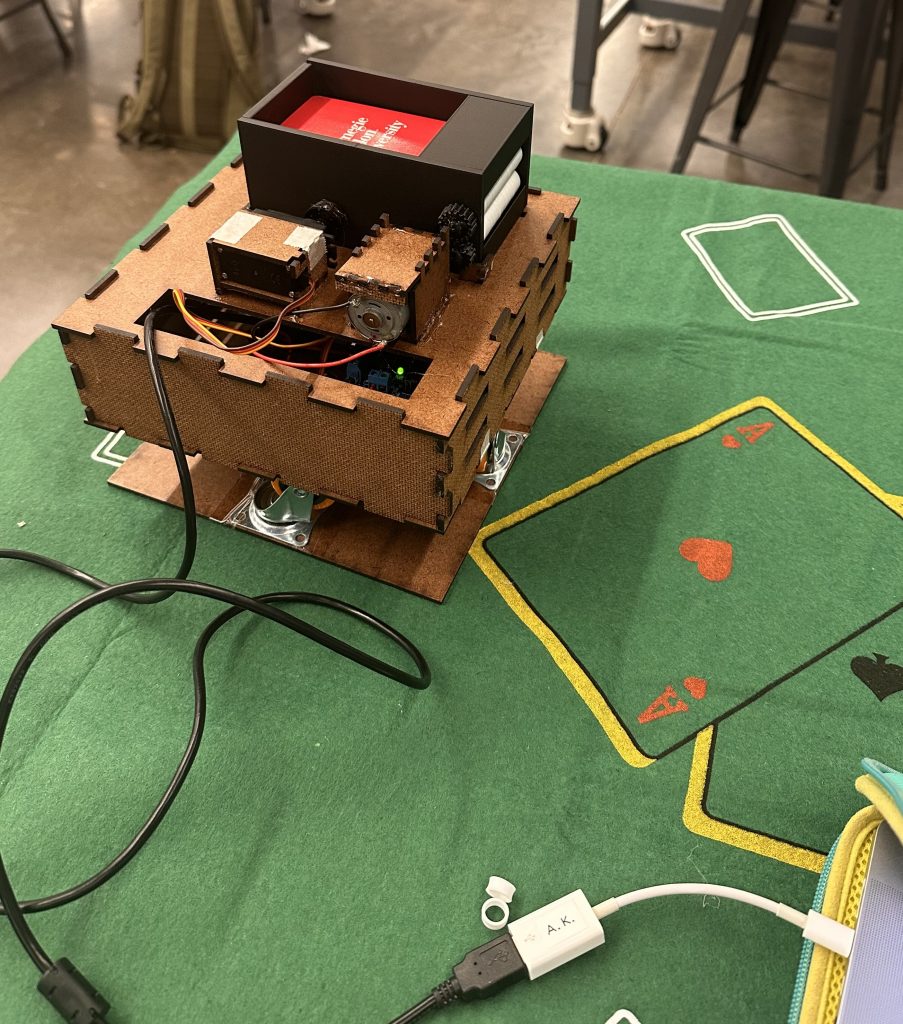
This is the semi-final machine body we have for now. It is only half-functional, because the cylinder connected to the servo does not move the card far enough, making it impossible for the two cylinders at the exit to grab it firmly and dispense it. We are going to add two gears (1:1.4) to the servo and the cylinder to increase rotation.
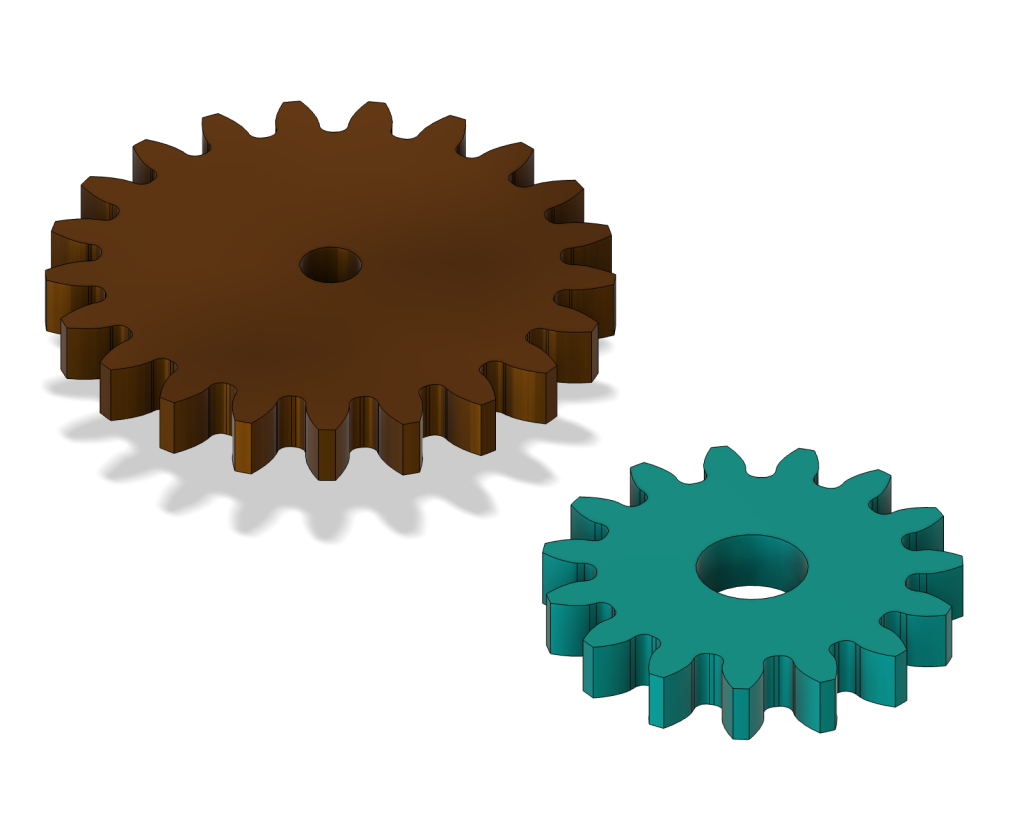
We were actually supposed to be done with this part already, so we are behind schedule right now. Hopefully, the gears get printed quickly, because integrating the gears into the machine should not take long.
I did confirm that everything else in the machine works perfectly fine, so once the servo issue gets cleared, it should be ready to be tested and verified.
We have a lot to do by next week. Hopefully, the RPi and Arduino won’t cause any trouble as we connect them.
Verification:
I will need to test the dispensing accuracy and machine rotation accuracy along with their latencies. Both tests have been done roughly, but the full quantitative tests still needs to be done. The size of the machine already meets the requirement of 20.3 cm x 20.3 cm.
Those complete the hardware and machine body side of the requirements that we have set.