- The most significant risk right now is bringing all the parts together. Especially with constructing the hardware, we have hit many situations similar to deadlock in real life. For example, we want to test out a component by attaching it to our rack, but then attaching to the rack is permanent so we want to test the component. This has slowed down a bit of our final parts list compilation. We plan to work dedicate most of our time in testing our components as well as possible next week. As for contingency plans, plan to be very flexible on researching and ordering new and different components in the event that our existing items do not work out.
- There are no changes to the existing design at this time
- Progress on the software has been a bit slow due to some unexpected business, but a countdown has been added to facial recognition to give the user some time to prepare themselves to get scanned, and a way to register new faces is currently in the works.
Current progress on the rack!
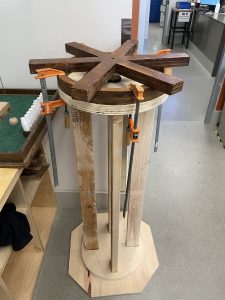
- A was written by Ryan Lin, B was written by Doreen Valmyr and C was written by Surafel Tsadik.
Part A: Our product solution is universal across global factors. There really isn’t specific skill or knowledge on how to use our system because we designed the system to be easy to use with limited user interaction. People all over the world go to events and need their items to be stored quickly and securely. One possible way that our product solution may not work with global factors is if our implementation is not all-encompassing. For example, faces in different countries around the world will look different and will be a challenge for our facial recognition system.
Part B: Our innovative product streamlines the often cumbersome process of checking in and retrieving personal belongings, particularly at events attended by large crowds. By leveraging facial recognition technology integrated with a physical coat rack system, individuals can swiftly deposit and retrieve their items, freeing up valuable time for social interaction. Crucially, our solution is designed to be inclusive and culturally sensitive, accommodating users from diverse backgrounds and belief systems. With no barriers to access, individuals of any cultural or religious affiliations can seamlessly utilize our product at events. Additionally, the non-invasive nature of our technology ensures widespread acceptance, as it simply relies on facial recognition for item storage, devoid of any controversial features.
Part C: Currently, many coat checks use a physical ticket system to store and retrieve items. Paper is usually used to print these tickets, and if the event has a large audience a lot of paper will be used and later thrown away. With our system, it will eliminate the need for physical tickets, meaning no more paper needs to be used to print said tickets. Less paper wasted means a positive impact on tree preservation, decreasing the number of trees we need to cut down to produce the paper that goes into the physical tickets.