This past week was primarily dedicated towards refining project requirements and better defining our design via system diagrams. We also focused on creating our Design Review Presentation (slides available on the Documents page).
Requirements Discussion:
The feedback we received from our proposal presentation and abstract mainly focused on the need for better technical requirements. While our “Wage” equation was an acceptable, if a bit cumbersome, measure of overall project usability, it was not a concrete enough metric to use for evaluating the technical success or failure of the project.
Over several meetings, the team established an entirely new set of technical requirements. We also refined our feature requirements, and our overall project requirements. The latter set of requirements, the project requirements, would be the overall measure of project success. This was originally the Wage metric, but the new list also pulled out simplified portions of the Wage equation as separate requirements. First, the yield ratio requirement would compare ratios of input seed weight vs. output produce weight of the MiGroBox groups versus manually-grown control groups. We settled on requiring the MiGroBox yield ratio to be no less than 85% of the manually grown group seeing as automated care of plants would likely be worse in quality than manual care – given error and losses in seed distribution, less accurate watering, and unnatural sunlight. The second results requirement was the raw labor hours reduction between the automated and manually grown groups. We settled on a goal of having a 30% reduction in time spent over the course of the week. This measure of time spent would include every repeatable activity involved in the weekly grow cycle: set up, seeding, care throughout the week, harvesting, packaging, and cleaning. Given that initial set up, harvesting and packaging (all significant time-sinks) were not part of the scope for automation, we decided that a 30% time reduction was a meaningful goal while remaining an achievable target. Finally, we refined our Wage requirement to be based off of our goals for yield ratio and labor hours reduction. First, we set a goal for the Wage to surpass minimum wage ($7.25/hr) to make the device reach parity with baseline American human labor hours. Running the numbers for wage differences based off of our acceptable yield loss and time gain (using a real, observed range of sale price rates) we set the expectation that the MiGroBox would improve wage by 20%.
The technical requirements were based off of prior goals, but delved more deeply into solid, measurable aspects of the project. We decided on five total technical requirements: Seed density/distribution, water spread/coverage/drainage, seed dispensing accuracy, watering frequency, and website latency. Seed density is essentially the distribution of seeds over any square inch of the grow tray. By requiring that the tray not have any areas overly clumped up, the thinking goes, we can ensure effective room for each seed to sprout thus maximizing yields. Analyzing grow data from Johnny’s Seeds, we found that significant reductions in yields occurred at roughly 33% higher-than-optimal seed density and thus set this roof as a requirement. Water spread, we decided would be required to reach 100% saturation of the grow medium essentially by definition (seeing as our watering method would involve soaking the grow tray, 100% coverage would be easily achievable). We added within this watering requirement that excess water would have to be drained from the grow medium within 20 minutes – our research showed root oxygen levels for microgreens would suffer if they remained submerged in standing water for any longer. Our final critical technical requirement, seed dispensing accuracy, required the weight of seeds dispensed by the storage hopper into the smaller seed distribution hopper to be within 1 gram of the target weight. This value was based off of our research of Johnny’s Seeds grow data (25-40 grams of seed per tray) as well as the granularity of the ESP32 ADC (4095 values). This 1 gram requirement would also take into account the worst-case for load cell sensor inaccuracies. The last two technical requirements were less critical but still important to note. First, the irrigation system was required to be capable of watering plants at least every 12 hours to achieve the needed twice daily watering cycle. Second, the traget website latency, measured as time-to-first-byte, was set at less than 2 seconds to remain usable while not adding pressure the the project. We noted in our research that this goal would make the website interface perform below the average of 1.2 seconds for desktop sites, but found this to be acceptable for our project.
Finally, the features requirements list was set as follows:
Climate control/monitoring: Irrigation; Lighting, Air circulation; Temperature Sensing; Humidity Sensing
Seed storage, distribution, and care: Long term seed storage; Seed dispensing; Seed rinsing and soaking; Seed distribution; Seed pressing
Seed grow regime pre-sets: Saved optimal values for at least the plant varieties grown over the course of the semester project
WiFi user interface: Custom website; Device connected to WiFi 24/7
The complete list of our project requirements (including explanations and reasoning behind each) can be found on the Documents page.
System Diagrams:
Aside from the extensive rework of project requirements, the week also included all the need preparations for the design review presentation. Chief among these was the generation of system diagrams:
The team stated by defining the software-hardware interaction focused around the device. The overall diagram we created also separated sensors from actuators while also grouping them by which feature they were a part of.
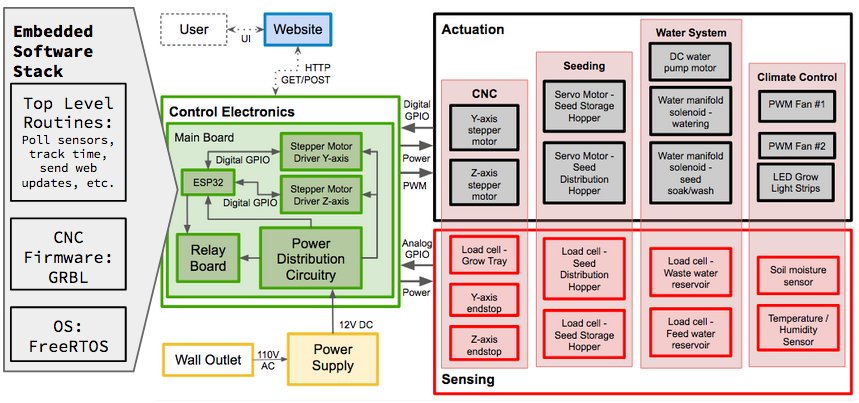
Lucas created a rough diagram of the physical layout of the device. While not representative of exact, final sizes for each component, this diagram served to express the way the components would be distributed throughout the box as well as the way they would move/interact. The diagram included the visualization of the “soak, rinse, distribute” zones the seed distribution hopper would move between:
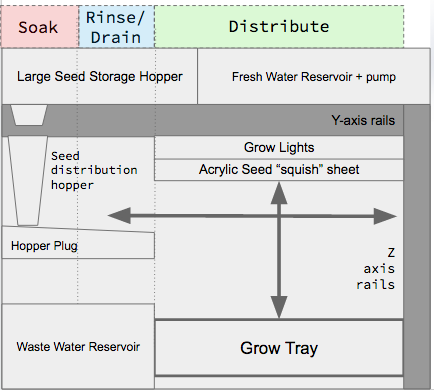
Greg refined the website interface design and laid it out in a separate block diagram:
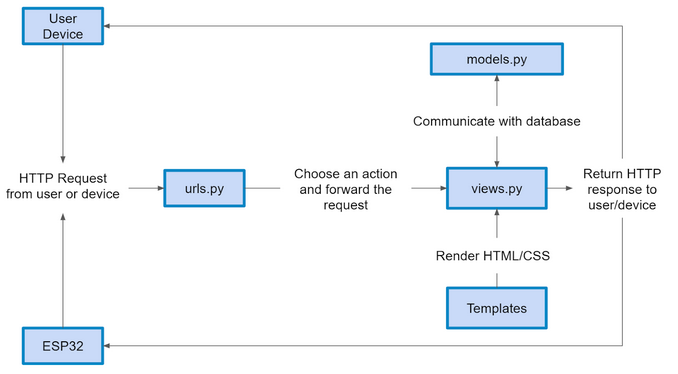
This week served to greatly refine and solidify the project scope and vision, but lacked concrete development work beyond the creation of diagrams. The following week will still be light on development work as it will focus on finishing the Design Report. The following weeks will see a flurry of work with CAD models being solidified, the website back-end being set up, and main board schematics being completed. The first team integration goal is to get the microcontroller, running FreeRTOS, plugged into a main-board prototype together with two stepper motor drivers and talking to our basic website interface.