The most significant risks as of now are getting the manufacturing and assembly of the enclosure finished by this week. Our manufacturing timeline had to get pushed back by one week, since we had some road bumps relating to material sourcing and selection last week, so we will put most of our effort this week into laser cutting and assembling everything to get back on track with the original deadline by next week. On the software + electrical sides, we were able to bootload the RPi and get it up and working, and in an effort to support the mechanical side of things more this week, we were able to finish the general layout of our GUI ahead of schedule. We had also originally dedicated some effort to submitting purchasing requests this week, but since we were also able to get that done earlier, we’re able to consolidate more efforts towards manufacturing as well.
Were any changes made to the existing design of the system (requirements, block diagram, system spec, etc)? Why was this change necessary, what costs does the change incur, and how will these costs be mitigated going forward?
Nothing significant was changed in our design; however, there were some small size changes made to our CAD enclosure – namely, making the dimensions a little smaller in an effort to reduce unused space.
Provide an updated schedule if changes have occurred. This is also the place to put some photos of your progress or to brag about a component you got working.

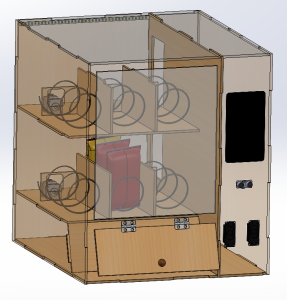
A was written by Ashira, B was written by David, and C was written by Anna.
Please write a paragraph or two describing how the product solution you are designing will meet a specified need…
Part A: … with consideration of global factors. Global factors are world-wide contexts and factors, rather than only local ones. They do not necessarily represent geographic concerns. Global factors do not need to concern every single person in the entire world. Rather, these factors affect people outside of Pittsburgh, or those who are not in an academic environment, or those who are not technologically savvy, etc.
Our vending machine’s design considers global factors in supporting user interface that is easy to understand and interact with. Our machine’s UI will be mounted will using a touch screen display, which will allow users to make selections and interact with the machine with steps and effort, an aspect that could be important for users who are not the most tech savvy. We also intend to include symbols and images during the timer & snack selection process in our GUI’s design, which would be important in cases where language or literacy barriers might arise. In addition, our vending machine’s notification system will include features which communicate a finished state through both visual notifications and sound as well, which is something that could be important for users who might be hard of hearing.
Part B: … with consideration of cultural factors. Cultural factors are encompass the set of beliefs, moral values, traditions, language, and laws (or rules of behavior) held in common by a nation, a community, or other defined group of people.
Our vending machine project considers cultural factors by ensuring accessibility, inclusivity, and user-friendly design. We use a touchscreen interface with simple language options to accommodate different users. The machine provides both visual and audio notifications, making it easier for people from different linguistic backgrounds to use. Additionally, we follow safety standards and design rules to meet different community expectations. If placed in a specific location, we can adjust product choices based on cultural preferences or dietary restrictions. By considering these factors, this is a vending machine that respects and serves a diverse group of people.
Part C: … with consideration of environmental factors. Environmental factors are concerned with the environment as it relates to living organisms and natural resources.
VendiBaddie takes environmental factors into account by considering the materials used in its construction, potentially reducing waste. The enclosure has been designed to be made of affordable wood panels which tend to be sturdier and more durable, ensuring longevity and minimizing the need for frequent replacements. Additionally, the machine utilizes a touchscreen interface which will effectively help with reducing the need for physical buttons or extra hardware by making the user interaction more flexible and thus lowering electronic waste in future iterations. While our current design does not prioritize energy efficiency, future improvements could explore the use of recyclable or sustainable materials, as well as energy-efficient components or alternative power sources to enhance sustainability and reduce environmental impact.