Risks:
The greatest risk remains getting all the different pieces of the project to fit together in the time we have. We’ve made good progress there, though moving forward we’ll probably need to coordinate more directly with each other as the parts of the project become more intertwined for the final product. Making sure we are effectively communicating with each other and our team advisors for this final venture seems to be the best way to avoid risk.
Design Changes:
We reintroduced the design requirement for furniture classification into our design. This required adjustments to the system requirements, updates to the block diagram to incorporate furniture classification components. This made it necessary to include a camera in our design to capture images of furniture in the room. Adding the camera did not introduce significant additional costs because we plan to use a camera from the 18-500 inventory.
Schedule Changes and Updates:
We adjusted the schedule to reincorporate the furniture classification section in the schedule.
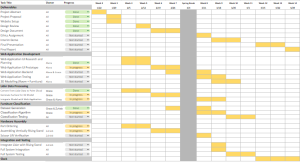
Weekly Questions:
Part A was written by Zuhieb, Part B was written by Alana and Part C was written by Grace.
Part A:
With the way we are developing TailorBot, we are aiming to provide a seamless user experience that would allow anyone of any background to interact with our product. TailorBot makes the time-consuming and physically demanding process of interior room designing accessible simply through a computer. This eliminates many existing barriers that prevent people from getting involved with the redesigning process, allowing anyone to use TailorBot regardless of knowledge, technical expertise, location, or physical ability.
Part B:
Our product has a small cultural niche, appealing to anyone interested in interior design. While not grand, it could help foster that community by making the interior design process easier for those outside of the professional sphere. It is not uncommon for communities to form around tasks or projects once reserved for big companies or wealthy individuals as the tools for them become more accessible. For an example, for a long time making video games was only feasible for big companies as they were the only ones with access to the funds and tech to do so. However, in the modern day, multiple successful game titles have been made by small teams or even one person as tools for game development have been made accessible and entire communities about game creation are out there to engage with. While TailorBot isn’t a game development tool, perhaps it could also help make interior design more accessible in a similar way.
Part C:
TailorBot is designed for sectors like interior design, real estate, and inventory management and it provides critical insights into space utilization and arrangement. This room scanning system encourages a more informed approach to space planning and furniture arrangement, promoting efficient use of resources and materials. By providing detailed 3D models and accurate furniture classifications, the system enables users to optimize space utilization, potentially reducing the need for unnecessary furniture purchases and encouraging the recycling or repurposing of existing items. This not only aids in minimizing waste but also supports sustainability efforts by advocating for more thoughtful consumption patterns.
The system’s design also provides environmental considerations. The use of a LiDAR sensor, allows for the rapid collection of spatial data without the need for the use of materials that could harm the environment. The system’s design emphasizes low energy consumption, with components like the Raspberry Pi and efficient LiDAR sensors minimizing the overall energy footprint.
Developments:
Overall, we had made some good progress individually and decided to add back the furniture classification system based on some feedback we got. Here are some pics of what we’ve done.
A scissor lift prototype:
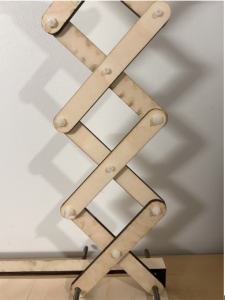
3D models in the web application:
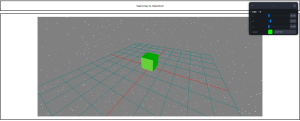