Progress
This week, I got numbers on the energy output of the motor, and we assembled the final watch.
After many difficulties trying to get the tolerances correct and having to adjust the gear ratio, I finally was able to attach the motor to my arm and collect data on its energy output. The data was very noisy due to the imprecision of my own motion, and I could only record for short periods of time due to the fact that I could not find the set of ball bearings I needed to keep the two halves of the gearbox in line. However, when the parts were aligned correctly, it swung very well and yielded 1-2mW of power output at what felt like a running pace. This is comparable to the power output of the paper we were referencing; the 50% loss in efficiency is likely due to problems with my mechanical design. With some refinement, this means the motor could be a viable energy source for the watch. However, the main issue is size; the current gearbox is the same as the size of the entire watch body, and to get it smaller would require integrating the rotor, stator, and gears into a single custom assembly. This could be interesting for further research, but for now it just isn’t viable.
Just yesterday we were able to assemble the final revision of the PCB. I did some modifications to the case design to make the PCB fit, assembled a small “debug header” with pogo pins to program the new board, and also ported over our code to work with the new pin layout. Amazingly, everything worked:
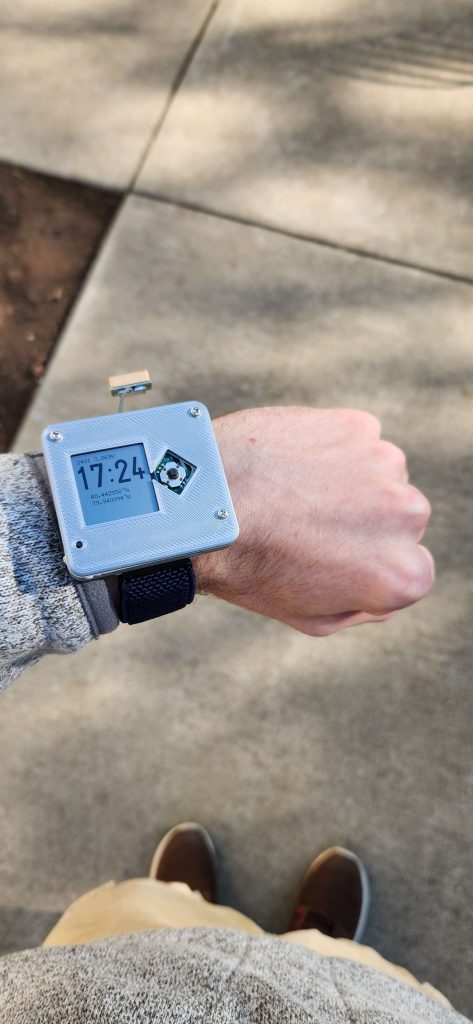
Learning
Over the course of this project, I had to learn many new things: low power circuit design, gear manufacturing, GPS protocols, SD card interfaces, debugger setup…
Many of the “formal” aspects of implementing these ideas came from reading research papers and datasheets—in particular, this is how I would get equations, design parameters, and circuit layouts, for determining at a high level how I should accomplish a task. Then, inevitably, while trying to do most tasks I would find that the high-level overview leaves out several steps, or doesn’t quite work in practice. This then usually lead me to Google, where I pieced together forum and blog posts from people with vaguely similar problems to see how I could solve my own. And, finally, I would sanity check my ideas with people I knew had knowledge–first my team members, and then my friends (in particular, it was quite hard to get mechanical engineering advice anywhere other than in-person).
Pacing
The only remaining item is the firmware, which is a little bit behind where I’d like it to be but is very much doable now that we have two sets of real hardware to test with.
Planning
Next week I will:
- Implement actual menu navigation
- Find a way to display the path the user has taken on the map
- Determine if there’s an easier way to use the USB bootloader on our final PCB