The risk of the pressure system remains the biggest as of now. We’ve noticed the pressure is not leaving the tube as quickly as we hoped and making adjustments, but the new design might still encounter this issue – we are exploring mechanical shooting mechanisms to mitigate this risk. The hardware’s stability is also an issue. As we’ve experienced hardware failure on the microcontroller this week, having spare parts to mitigate this is going to be important.
We have no major design changes this week.
We’ve updated our Gantt chart this week to match the progress we’ve made. The cup detection and the pressure system has been moved back a little bit, and some of the workload has been re-distributed. The updated Gantt chart is attached below:
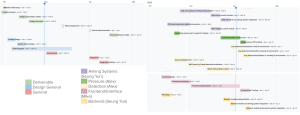
As we approach the last stretch, we have multiple verification and validation plans in place. For verification, as discussed in individual reports as well, the aiming subsystem will perform a series of movements and take physical measurements to verify it works.
For the validation, once all systems are built, we will test the system by launching the ball in the same setting 10 times to a grid paper, and note where it landed. As mentioned in design presentation previously, if we can draw a 2cm * 5cm bounding box on all the landing spots, we will have successfully validated our project.
For the computer vision ball detection validation, we will measure the accuracy by positioning the LIDAR sensor facing up. Then we will throwing a ball over the LIDAR sensor and record where it lands on the ground. We will then compare the actual landing location to where the LIDAR predicted. We will then measure the absolute magnitude of the difference between the two points. We currently plan on doing 50 trials.
For the computer vision cup validation we plan on setting up the cups and then moving the cups around and measuring the distance between where the cups are predicted to be and where they actually are, similar to the method used for ball detection. The main difference here will be that we need to map out in 3d space where the cups are relative to the LIDAR so it will be more of a pain to set up, but once we have our measuring set up and validated, we will be able to quickly collect data.