Potential Risks and Risk Management
We have finished 3D printing the necessary components this week though we anticipate issues that may lead to reprinting. We will be inspecting each printed component this weekend and reprint at the Roboclub facilities on campus as needed. Running out of 3D printing filament is the least of our concerns at the moment as our Amazon purchase bundled four rolls together, whereas we are only using one at the moment.
Additionally, upon inspecting the Arduino schematic we noticed that we will also have to plug in our DC power source (supplying 12V) to the Arduino’s “Vin” port for power. Initially we feared that the supplied voltage would overwhelm the Arduino but upon closer inspection, it would appear the Arduino is capable of withstanding a maximum of 12V. Regardless, as the voltage we are supplying is the maximum, we are considering powering the Arduino using the data port with the Jetson to circumvent potential pitfalls. The Arduino will still be grounded with the remaining electronics.
Furthermore, we believe the alligator clips found on campus are incapable of withstanding the higher voltage and current necessary for powering the DC motor driver. Therefore, we will be soldering higher gauge wire onto the purchased male to female wire.
Overall Design Changes
There have been no major design changes since our last status report. We will likely be adding a breadboard to better manage the wiring of the actuators with the Arduino, though the overall wiring should remain the same.
Schedule
Currently, there are no major updates to our schedule. However, we have updated it to indicate our progress on ongoing tasks.
Progress Update
This week, we were able to drive the servo with the Arduino 5V with hardcoded classification signals.
The goal is to establish communication with all devices (Arduino, Jetson, Motor, Servo) by the end of the coming week. Over the weekend, we plan to integrate the classification signals into this infrastructure to drive the components accordingly in time for the interim demo.

Additionally we have started work on the mechanical build of the project. We sliced the metal parts in TechSpark and began 3D printing the necessary components. We hope to continue assembly to have a partially functional product in time for the interim demo.

Regarding the model, we have started fine-tuning this week. We are utilizing the training files pre-defined by Ultralytics for YOLOv5 (yet another benefit to adapting a YOLO model), which comes with some neat visualizations as shown below. We are fine-tuning our model to improve its performance with regards to not only accuracy but also reducing false results, which can be more accurately judged via the precision and recall metrics provided by the script.
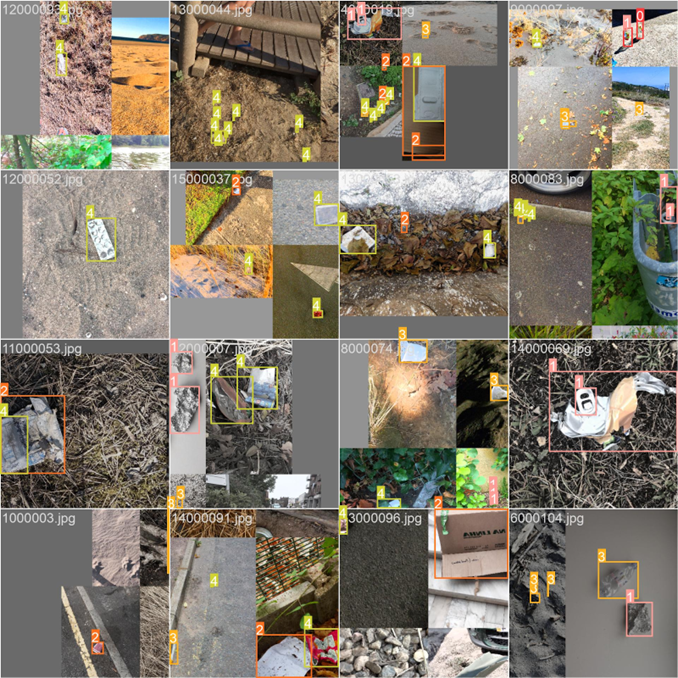
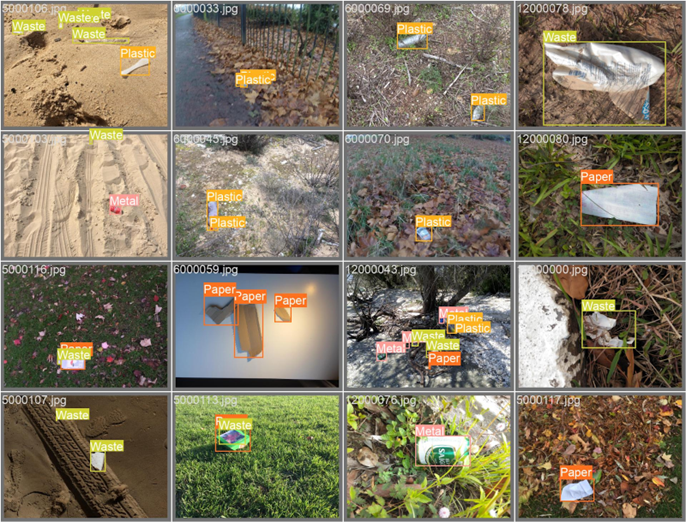