This week we began optimizing our system to look more visually appealing for the eventual final demo, now that we have a working system end to end. We began by shortening the pipes and taping the valves to our wooden structure so that the flow rate is consistent and the dispensing system looks cleaner. We also scaled out to 6 bottles and numbered them in certain positions on the dispensing unit that map directly with the website ingredients. Additionally, we improved the AI recommendation service to fully output customize drinks based on variety of user input and added in a “fun fact” which is additional information on the drink being made. Furthermore, we printed out the platform that the cup will sit on and the stirring mechanism will rest beneath. Finally, we scaled out the circuitry that attaches to each valve such that now we can control 6 different solenoids related to the 6 ingredients.
Below is the image of attaching the valves to the wood: https://drive.google.com/file/d/1NUxk5qAmYsefShDEVbOFaYRmuMOm26_l/view?usp=sharing
Below is the image of scaling out the circuitry: https://drive.google.com/file/d/1aPcGPDX6_HwjfodIvGQHIX_9pdHxlQD1/view?usp=sharing
Below is the full image of all valves attached to the system: https://drive.google.com/file/d/1G9PB19FqwNt-jJ9HlFJwAHforfFz5lIG/view?usp=sharing
Verification and Validation
In terms of testing the dispensing system, we are currently in the process of testing amount of mL dispensed and mapping it to timings the valves are open to ensure the right amount of each ingredient is poured. We are testing this by individually measuring dispensing amounts using a measuring cylinder and currently experimented with two different valve pressures to determine which one gives a steady and reliable flow. We also are planning to run several trials to observe and minimize leakage, using specialized safety clamps to observe where leakage is happening and avoid it. Finally, we are planning to do many different combinations of ingredients using the inbuild ingredients page and AI recommendation service to ensure certain valves correctly open. We plan on measuring the final amount of product and ensure it matches the sum of the ingredients also using the measuring cylinder.
In terms of the mixing system, it is pretty simple and reliable in its mechanism, so testing will be a series of repetitions in the overall system, ensuring that the pill spins for a certain number of revolutions for sufficient mixing. This number will be determined later after several trials of experimentation.
In terms of the garnish system with the robot arm, we currently have it fully integrated with the rest of the system but plan on testing individually to ensure the robot arm can reliably place the garnish in the cup. To do so, we plan on transitioning to the actual garnishes we are going to use for the demo, and test the robot arm on all the different ingredients multiple times, to ensure the robot arm and clamp is configured to pick up these unique shapes.
As a system altogether, we plan on running several tests using different combinations of ingredients, amounts, garnish selections to ensure the robustness of our system. We also plan on experimenting with different orientations to validate the quality of the system in an external enviroment.
Status: On schedule
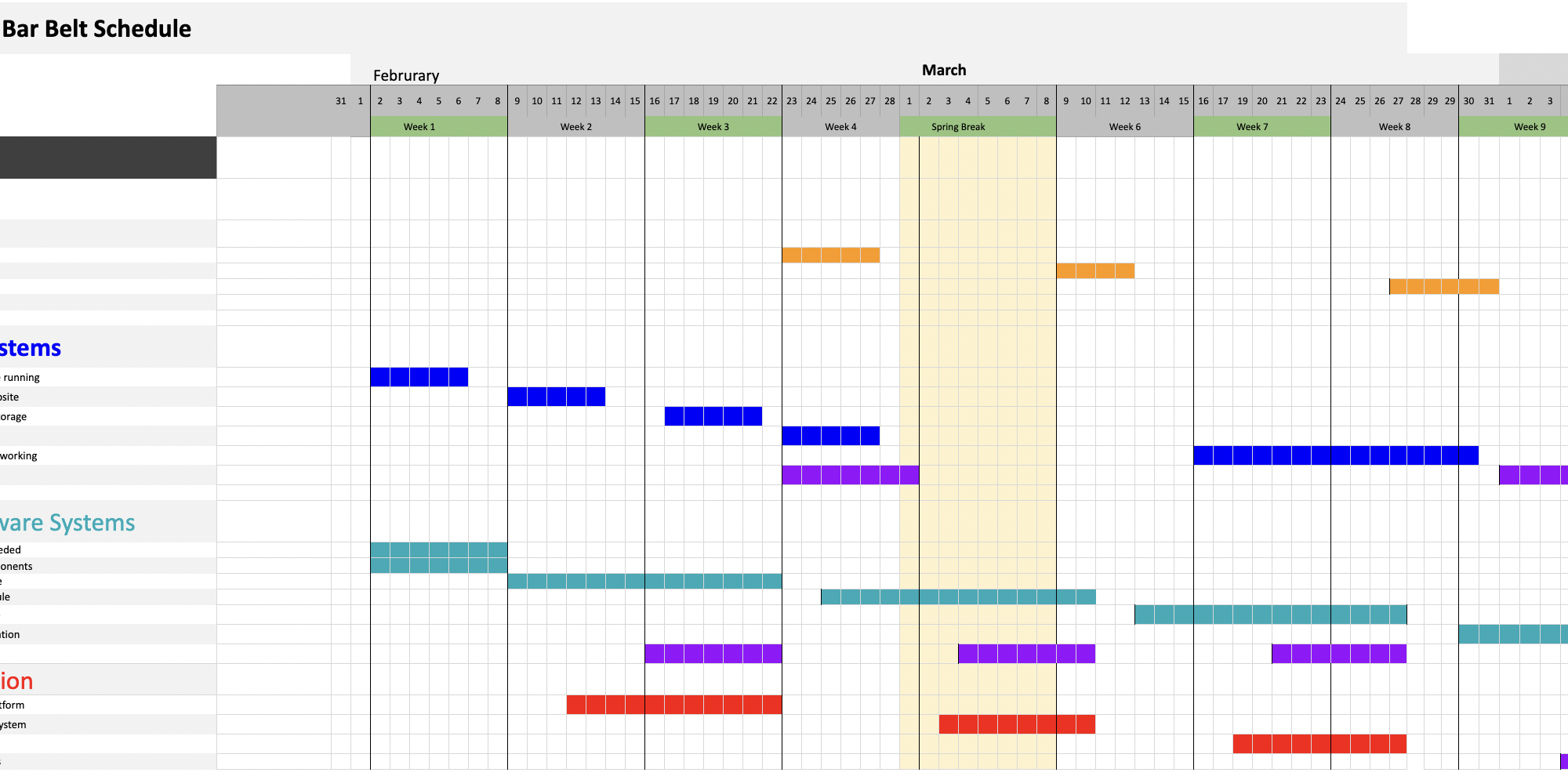