These two weeks we basically worked on writing the design report. Based on feedback and discussion with professors, we decided to rewrite our use case. Also, we added a lot more design details about how we would connect each components physically. We ended up ordering many new components for the project. Personally, I am staring to set up Raspberry Pi and wrote some pseudo code. I now have some overall idea about how my code would look like, but I still need to learn how to send correct signals to stepper motor drive. Below is a screenshot of part of the pseudo code. 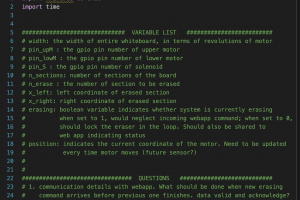
Due to changes in our design, we ended up ordering some new components during mid-semester break, which might arrive later than expected. Some of my code would need to depend on the components, so my schedule might be behind. However, I am planning to start writing code about whatever I have now, and spend some extra time fixing everything once our new orders arrive.
Next week, after the components arrive, our team will be spending much time on physically building the system and adjusting it. Personally, I will also continue to write motor and solenoid control code.
In response to the weekly question, I am learning to use Raspberry Pi for this project. I’ve had previous experience with Arduino and Nucleo microcontrollers, so I expect that learning to use RPi would not be too difficult. Another thing that I need to learn is to use stepper motor driver, which might differ from regular DC motor drivers that I used before.